Freeing Up Staff Time with Streamlined One-Stop-Dispensing
Case Study - How the part pack feature of Omnicells’ Universal Logistics Management (ULM) streamlined one-stop-dispensing and has freed up staff time
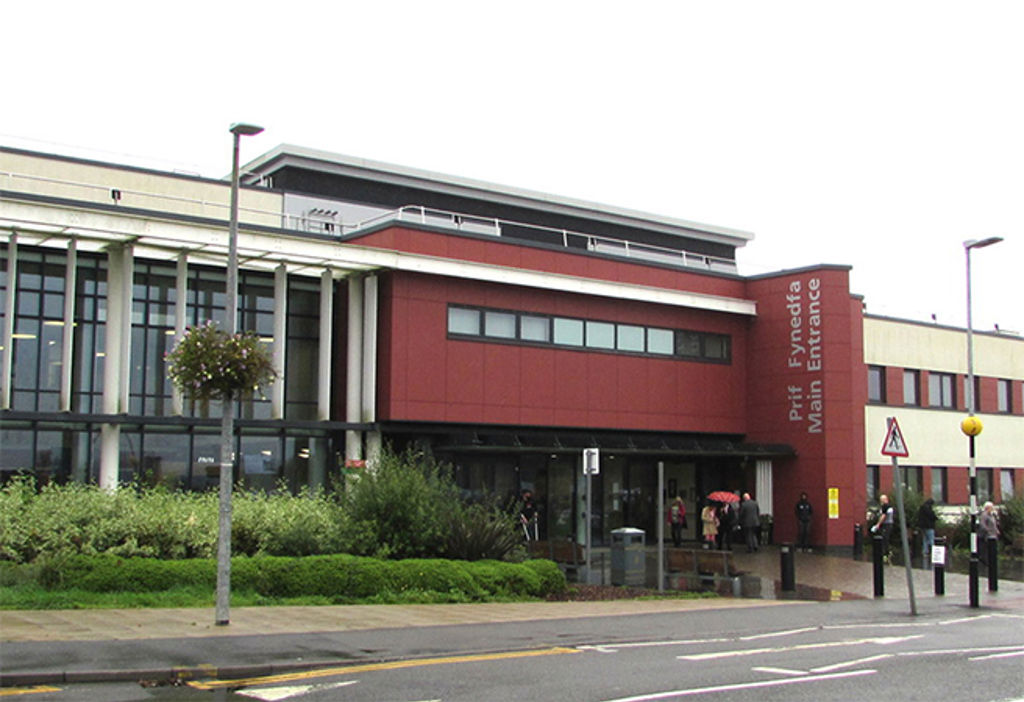
-
Site
Morriston Hospital
-
Equipment
ULM
-
Department
Hospital Pharmacy
Context
The central pharmacy has been moving towards a technician-led organisation in the past years. Automation and two Omnicell robotic storage systems have helped to smooth the pharmacy’s workflow and have resulted in faster work turnaround.
Challenges
- Returning part packs is time consuming and error prone
- Time spent on operational and repetitive tasks
Benefits
Reduction in return time
From 1 hour to 30 minutes to return 40 packs after ULM installation.
Reduction in medication waste
Teams can easily find out if a medication pack has already been opened, therefore a new pack is only opened if required.
Significant Savings
Significant time savings, cost savings and reduction in increased splitting waste.
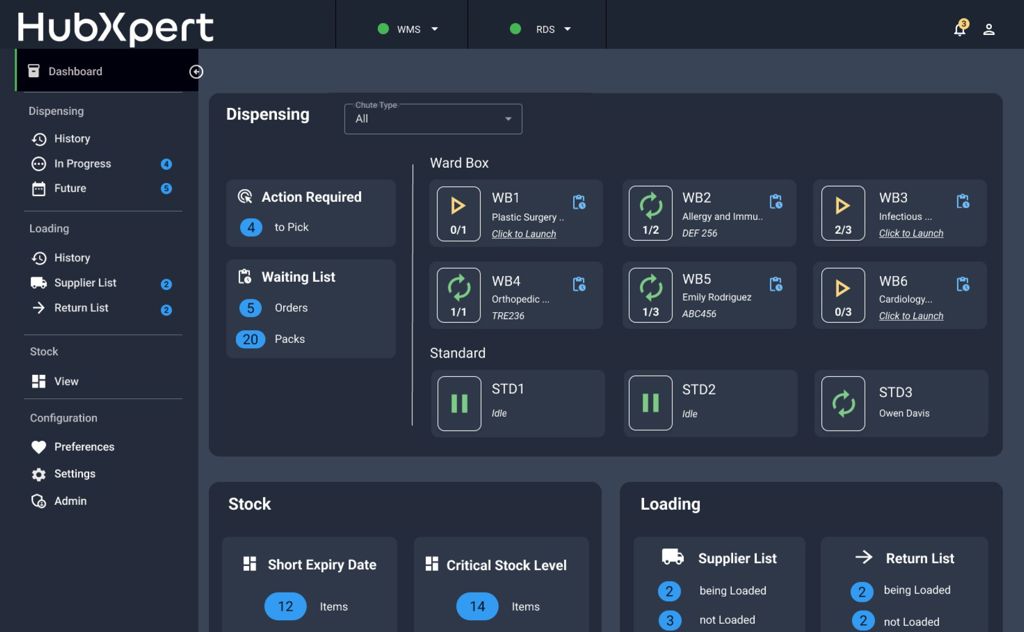
Your Journey to an Autonomous Pharmacy Starts Here
We're working with over 100 NHS Trusts to reduce errors, waste and workload. Contact us today to kick start your automation journey.
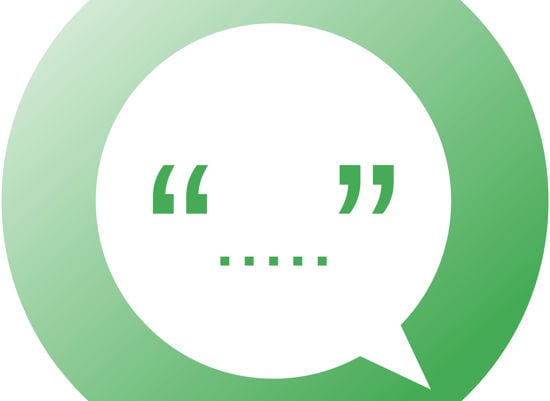
We are really happy with the new process.
Time Savings
50% Time Saving
Time it took to return 40 packs to the robot before the implementation of the ULM: 1 hour.
Time it now takes to return 40 packs to the robot after the implementation of the ULM: 30 minutes.
Reduction in Increased Splitting Waste
As Omnicell robot dispensing system stores and manages the part packs, the team can easily find out if a medication pack has already been opened, therefore a new pack is only opened if required.
New Process Leads to Savings of £7,171.25 per Year
on personal with a ROI within less than 3 years.